What Is Tool Steel?
Tool Steel is widely used across the world by a range of toolmakers, engineers and pattern makers. Tool steel is not one particular steel, as it refers to a range of carbon alloy steels. The different grades are popular due to their unique hardness, resistance to abrasion and, more importantly, the ability to withstand high temperatures and retain their cutting edge or shape.
Tool Steels contain four major elements, including tungsten, chromium, vanadium and molybdenum. Depending on your toolmaking project, you will require a tool steel grade containing more or less of the desired elements. For example, if the tool steel contains additional vanadium, it will be more corrosion resistant.
Due to their resistance to high temperatures, manufacturing and engineering industries use tool steels to cut and press metals and other materials. Furthermore, tool steels are often used as part of the final product.
How is Tool Steel made?
Tool Steels are made in various ways, although you’ll find that they all use one similar process. That is that they’re always produced in controlled environments to achieve maximum quality.
Tool Steels typically contain 0.5% to 1.5% carbon content. However, the manufacturing process introduces other elements such as tungsten, chromium, vanadium and molybdenum. The most popular steel production processes include:
Rolling
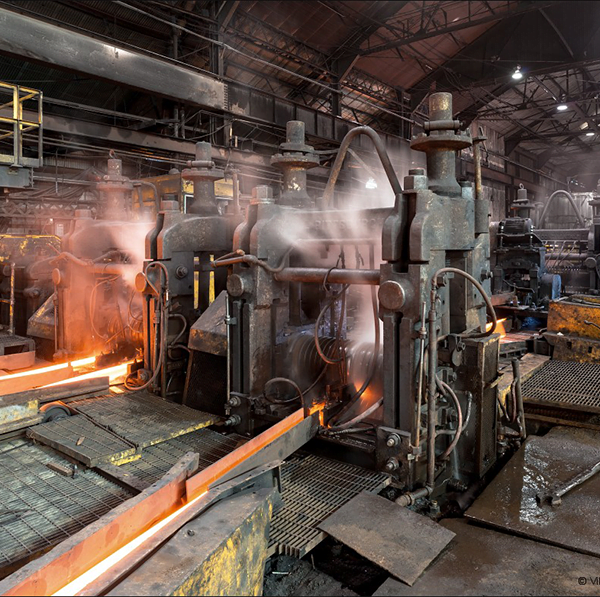
Rolling mills are used in the steel forming process in which steel is passed through the rolling mill to give the steel its desired thickness. This process is usually achieved with hot rolling, as with each roll, the manufacturer will press the steel a little thinner.
Primary breakdown
A primary breakdown is a fantastic option for tool steel producers when high quality and little to no imperfections are required. This process works by using either an open-die hydraulic press or rotary forging machine.
Hot and cold-drawing
Hot and cold drawing is used in the tool steel production phase to increase durability, produce smaller sizes and unique shapes.
Tool steels offer extremely high strength (which is why they’re so popular). However, this strength means cold-drawing is limited to a single light pass to prevent the steel from cracking.
Electric arc furnace melting
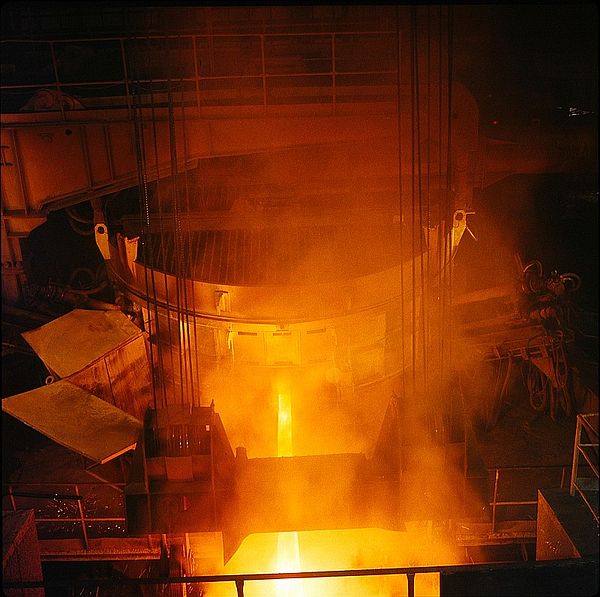
Electric arc furnace (EAF) melting, otherwise known as primary melting. This process works by heating metal materials using an electric arc.
According to substech.com, “approximately 33% of the worlds crude steel is made from EAF.”
Powder metallurgy
Powder metallurgy is a unique metal-forming process that helps to produce tool steels that are highly alloyed. The powder metallurgy process works by heating compacted metal powders to just below their melting points.
Unfortunately, powder metallurgy has a slow cooling time and low toughness compared to other methods.
How to choose the correct Tool Steel?
When choosing the correct tool steel for your project, you must factor in a range of different aspects. Tool steels are excellent for applications such as cutting tools, cams, dies, gauges, drill bits and knives. However, you may wish to use different tool steel depending on which you are manufacturing. For example, tool steel comes in multiple forms, such as water-hardening, cold-working, shock-resisting, high-speed and hot-working. You will also find different grades within these types, which will be more suitable for your project.
Some of the most common questions you should ask yourself include:
What is your budget?
Tool steel grades vary massively on price, with water-hardening usually offering the best price available. Low-budget operations will want to look into tool steel grades such as W1, W2, and W3. Nevertheless, these may not be the correct steel for your application, so thorough research and discussion with a steel stockholder is needed before purchase.
What is the required working temperature?
If your project requires the application to work at high-temperatures, you should look into hot-work tool steels. These grades of tool steel will include higher amounts of tungsten and molybdenum. Make sure to look for grades such as H11 and other H series grades.
On the other hand, if your project requires applications to work at low temperatures, you’ll need cold-work tool steel. These options are usually the most costly but have fantastic mechanical properties to make up for the cost. Examples of this include D2 and O1.
Do you plan to use it for plastic moulding?
If you plan to use your application for plastic moulding projects, we’d recommend focusing on P20 or any other P series of tool steel. The plastic moulding requires a special type of tool steel that manufacturers can’t use for any other application type.
Types of Tool Steel
Tool steels are categories based on their features and abilities, for example, how tough the steel is, it’s working temperature, cost and resistance to shock.
These groups can be categorised into the following:
- Water-hardening
- Cold-working
- Shock-resisting
- High-speed
- Hot-working
For more information on the products we have on offer throughout these tool steel categories, call (+44)114 233 5291.
Tool Steel Grades
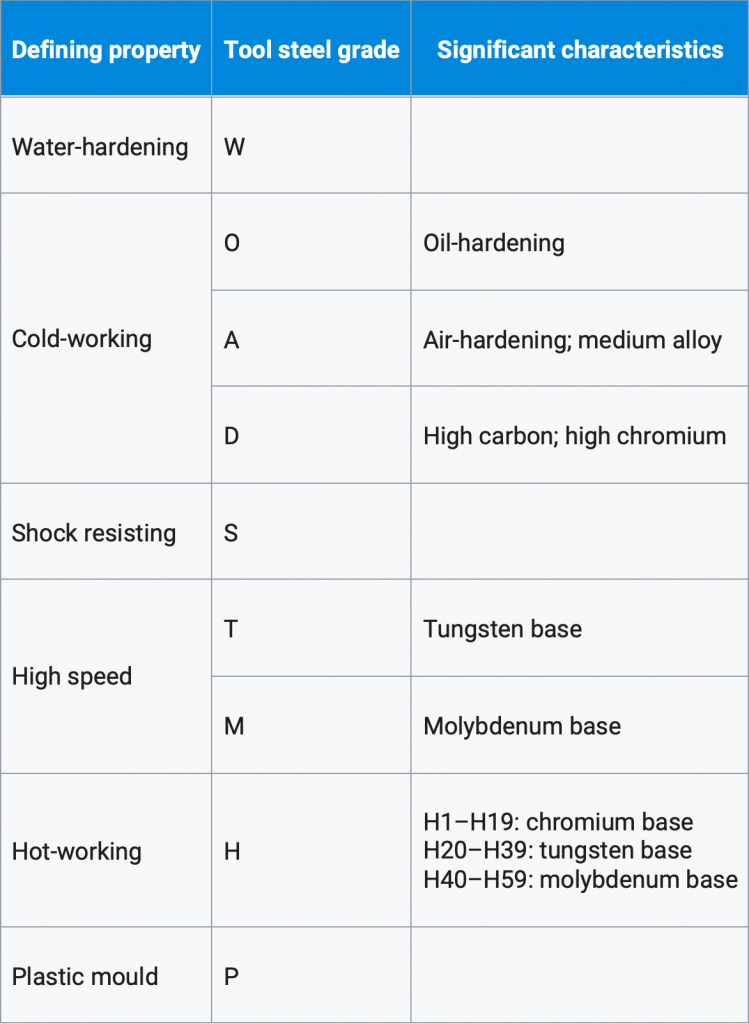
Water-hardening
Water-hardening tool steels can also be categorised as cold-working tool steel. As the name suggests, the water-hardening tool steels have to be water quenched. Otherwise known as W-grade steel, the undergone water quenching can lead to increased cracking and warping. This grade of tool steel is used less and less these days. Although, typical applications include (depending on the carbon composition) chisels, hammers, scrap shear blades, razor blades and small drills.
Cold-working
Cold-working tool steels are made up of a few different families, such as O-grades, D-grades and A-grades. As the name suggests, cold-working tool steels are used to form applications that are used at low-temperatures. Within these tool steel grades, you’ll find more alloying elements compared to water-hardening steels. These steels offer adamant wear resistance and machinability. Applications include cold shear knives, gauges, chipper knives, dies and knurling tools.
Shock-resisting
Tool steels that fall under the shock-resistance category have the ability to withstand great shock and provide good hardenability. This is achieved due to the chromium-tungsten and silicon-molybdenum. Not surprisingly, applications for the S-grades of tool steel include jackhammer bits, chisels, clutch parts, cold and hot shears.
High-speed
High-speed steels (HSS) are created from several metals containing a large amount of iron. High-speed steels withstand their hardness at high-temperatures and allow them to cut faster than other tool steels. Typical applications for HSS include power-saw blades, drill bits and gear cutters.
Hot-working
Finally, the last tool steel grade involves hot-working tool steels. These steels can withstand much higher temperatures than alternatives and were developed to maintain extreme strength and hardness at these temperatures. Hot-working tool steels refer to the H-grade of steels that contain a substantial amount of carbide. Applications for hot-working steels include casting dies, hot forging, hot gripper and hot shear knives.
Sheffield Gauge Plate
Sheffield Gauge Plate is one of the most leading suppliers of tool steel in the UK and worldwide. So far, we’ve supplied over 22 countries with our tool steel in various forms such as bars, tubes, sheets, plates and ground flat stock.