What is Rockwell hardness?
If you’re in the steel industry or simply looking to find the right type of steel for your tools, then you will have seen figures like RC60 or 45HRC. But what do these letters and numbers represent, and why is it important?
This article discusses what is meant by Rockwell hardness, the measuring process involved, how to understand the Rockwell scale and its application in determining suitable materials for their intended purpose.
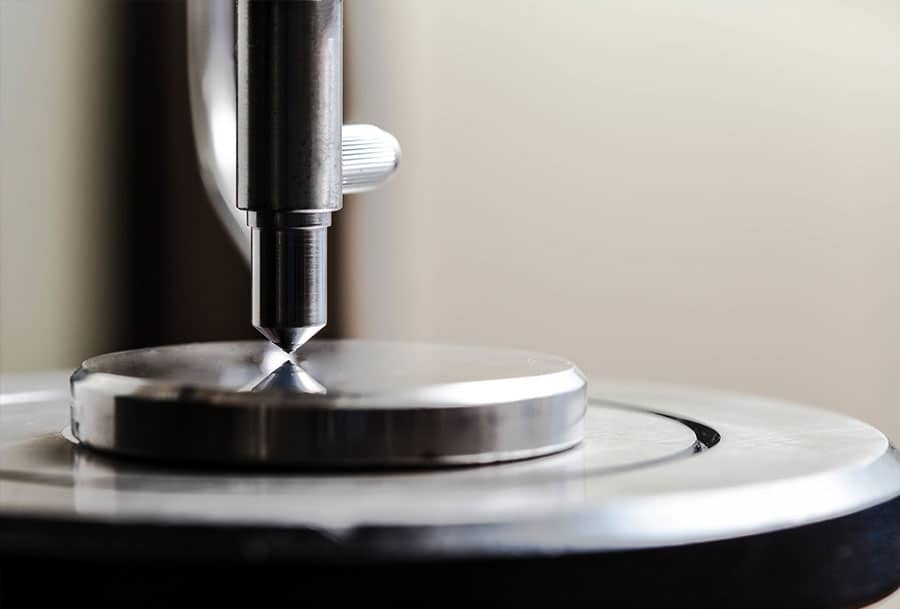
What is hardness?
Before delving into Rockwell hardness in particular, we must first understand what is meant by the term ‘hardness’. Hardness is one of many characteristics used to determine the overall durability and abrasive resistance of a material. It is a physical property defined as the ability to withstand surface indentation or localised plastic deformation. Generally speaking, it is a measure of a metal’s resistance to abrasion, scratching and indentation.
Why do we measure hardness?
Hardness is an important property to measure as it is an indicator of durability; the higher a material’s hardness value, the more resistant it is to wear and tear. Applying hardness testing to steel, or any material, allows you to determine whether or not it is the most suitable medium for the intended application. For example, if you need a malleable metal to make utensils, you wouldn’t choose one with the highest hardness value as it would be brittle and challenging to work with.
Overall, hardness is a significant factor you need to consider when selecting the most suitable materials for a particular purpose. To determine a hardness value, you can perform several tests, including the Rockwell Hardness Test, the Brinnel Hardness Test, Microhardness, Knoop, Vickers, and the Superficial Rockwell. In this article, however, we are focusing purely on the Rockwell Hardness Test.
What is Rockwell hardness?
Rockwell hardness is a series of indentation tests used to generate a standardised scale of hardness known as the Rockwell scale. The Rockwell testing method is widely used as it is highly versatile and relatively simple compared to other testing methods. It is often favoured commercially due to the speed and reliability of the tests, and it is also non-destructive. Materials can be tested numerous times without damage which is beneficial for heat-treated materials; for example, these will often require multiple tests before, during and after treatments. Other testing methods may result in damages caused to the test material.
How do you measure Rockwell hardness?
The Rockwell Hardness Test
The Rockwell hardness test involves a mechanical operation where an indentation tool made of diamond is placed against the test subject. Then, a preliminary force is applied, and the indentation depth is measured. Next, the total force load is added, with the indentation depth measured again. The total force load is then removed, so only the preliminary force remains in action. The difference between penetration depth before and after the total force is applied is then used to calculate the Rockwell hardness number. The Rockwell Hardness number is calculated by the equation:
100 – (H/0.002) = Rockwell Hardness number
Where H = the depth of indentation in mm.
For a brief demonstration of the Rockwell hardness test, watch the video below.
For more information about how we measure hardness and the range of steel products we have available, call (+44)114 233 5291 today.
How does the Rockwell scale work?
There are multiple scales to use when following the Rockwell method of hardness testing. Which scale to use depends on which type of indentor you use and the load you apply. For example, the Rockwell C scale uses the diamond cone shape indentor, and the B scale uses a ball-shaped indentor with a lighter load. The scales are abbreviated to HRB, standing for Hardness Rockwell B, and the same for the C scale (HRC). This is sometimes further abbreviated to just the letter R, followed by the scale letter (RC).
A general rule is that the higher the number, the harder the material – however, it is essential to remember that the hardness figures are relative to the scale used when testing them. To demonstrate, a soft steel may have a hardness of 70 HRB, while a hard steel may have a hardness value of 64 HRC.
Identifying the correct scale for the material you are testing can be difficult, but generally, the softer the material, the lighter you want the load to be. The same goes for thickness; if you have a thin material to test, you don’t want to choose a scale with a large indenter and heavy load as it will damage the test piece. Typically, if you are measuring hardened steel, you would apply the Rockwell C scale. Ideally, you would use the E or F Rockwell scale for softer materials as these have much lighter loads.
Scale | Indentor | Total Load (kg) | Typical Application |
A | Diamond cone | 60 | Thin steel, shallow depth case hardened steel, cemented carbides |
B | 1.588mm steel ball | 100 | Copper alloys, soft steels, aluminium alloys, malleable iron |
C | Diamond cone | 150 | Steel, hard cast iron, malleable iron, high depth case hardened steel |
D | Diamond cone | 100 | Thin steel, medium depth case hardened steel |
E | 3.175mm steel ball | 100 | Cast iron, aluminium and magnesium alloys, bearing metals |
F | 1.588mm steel ball | 60 | Annealed copper alloys, thin soft sheet metals |
G | 1.588mm steel ball | 150 | Phosphor bronze, beryllium copper, malleable iron |
H | 3.175mm steel ball | 60 | Aluminium, lead, zinc |
K | 3.175mm steel ball | 150 | Soft bearing materials |
History of Rockwell Hardness
Who invented the Rockwell hardness test?
In 1914, Hugh M. Rockwell and Stanley P. Rockwell (surprisingly unrelated!) recognised the need for a quick and effective test used to measure the strength of materials. While working together at a ball-bearing factory in Connecticut, they realised they needed to find a standardised method for measuring the effects of heat treatment on their steel bearings.
The pair of inventors set about creating a testing method that was non-destructive, cost-effective and easy to implement – and that is precisely what they did. Over 100 years later, the Rockwell hardness test is arguably the most prominent testing method used today and will continue to be for years to come.
Alternative ways to measure hardness
Although the Rockwell method is the most widely used hardness testing method, it is not the only method for determining hardness.
Brinnel
The Brinnel method was devised in 1900 by Swedish engineer Johan August Brinnel. Brinnel’s approach also involves indenting a material and using this figure to determine the overall hardness value. However, instead of a small diamond, the indentor used is a steel ball; the resulting larger indentation causes a damaged test piece that is no longer fit for purpose. It may have been the first standardised example of hardness testing, but the invention of the Rockwell method meant that Brinnel’s test was no longer the most effective way to measure a material’s hardness.
Vickers
The Vickers hardness test was developed in 1921 by Robert L. Smith and George E. Sandland. They set out to create a simpler version of the Rockwell test while still following the same overall indentation method. Differing from the Rockwell method, the Vickers test uses universal indentors and applies pressure for longer. Although the Vickers test can be applied to a broader range of materials than the Rockwell method, it is not the most common hardness-testing method. This is because it takes a long time to generate data, the indentation process damages the test material, and the equipment needed for the test is costly.
Steel Types and Hardness
Tool Steel Hardness Values
We are tool steel suppliers for the UK and worldwide. Our tool steels are manufactured under carefully controlled conditions to guarantee the highest quality results. The table below shows the tool steel grades we supply, with their Rockwell hardness values and uses.
Steel Type | Hardness (Max) |
O1 | 65 HRC |
W1 | 68 HRC |
A2 | 62 HRC |
D2 | 63 HRC |
S7 | 58 HRC |
M2 | 65 HRC |
H13 | 54 HRC |
V44 | 42-46 HRC |
A8 | 60 HRC |
1018 | 13 HRC |
O6 | 65 HRC |
4142 | 30 HRC |
1144 | 22 HRC |
View our helpful guide on how to choose the correct tool steel, or if you’re still unsure, contact our friendly team of experts who will gladly answer your questions and help you find the right tool steel grade for your intended use.
Machine Knives
Our high-quality steel makes us the UK’s best manufacturers of machine knives and blades. We apply our years of experience and knowledge to the highest standard materials to create a range of machine knives, including scrap shear blades, guillotine blades, demolition and construction blades, and granulator blades.
Ground Flat Stock
The ground flat stock we manufacture goes through the same quality-controlled procedures as the rest of our products to ensure high hardness levels and durability. At Sheffield Gauge Plate, we have been manufacturing the highest quality ground flat stock for over 40 years. We stock a wide range of standard sizes to suit all needs. However, if you’re after non-standard dimensions, we can produce these on request; enquire via telephone on (+44)114 233 5291, or email our service team at sales@sgpltd.co.uk.